一般的には最低でもn=30は必要とされています。
自動車産業では、各メーカーが部品メーカー(サプライヤー)に対して、求めているn数となります。これは自動車メーカーがサプライヤーに対して出している、取引先の品質マニュアルという100ページ以上ありそうな要求内容を読むと書かれております。
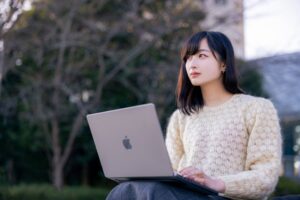
できればN数は、100以上が望ましいのですが
サンプリングが難しいものもあります。例えば巨大な部品とかの場合、工程能力評価のためだけに、100も製造することは困難でしょう。
その場合、一つの品番(サイズ)だけでなく、複数のサイズで工程能力を評価する裏技も存在します。それは後々教えることにします。
n数が少なくなればなるほど、データの信頼性は落ちます。その場合は区間推定といって、簡単に言えばn数を少なくすればするほど、工程能力のCpkの値を厳しく設定しなければならない手法を用います。
それでも面倒な場合は、一番シビアな品番で工程能力を算出する良いです。もっとも悪そうな品番で工程能力が良ければ、工程全体としてもよいパフォーマンでしょう。
もちろんサンプリングは、無作為に行う必要があります。具体的には無作為の連続ロットから抽出するのです。
よさそうな条件から抽出するのはよくありません。
一番ずるとしてありえるのが、n数は30として工程能力を算出するのに対して、サンプリングを40個くらいから行い、外れてそうな10個のデータは除外して、まともな30個から工程能力を計算するやり方です。
これでCpkが本当は、0.7くらいなのに、見かけ上1.0を超えたりするのです。
もし測定器で長さや重さを自動で計測しており、その測定結果の記録(データのログ)がマシンや端末上に残っていたら、そこから無作為に連続データで抽出して、工程能力を算出するのが、一番客観的なやり方です。
人出で測定すると、例えばノギスで長さとかを測定すると、規格値ギリギリ外れたデータは、意地でもスペック内に入れてしまおうとして、記録を書いてしまうこともなくもありません。これが人間の心理というものです。
特に上層部や、経営層が数字だけの、工程能力のデータだけに踊らされることがないように、普段から、監視体制も敷いておくなど、組織内でのガマバンス体制というものを構築しておかなければなりません。
そうしなければ、何が正しくて、何が正しくないのか把握することすらできなくなってしまうものです。